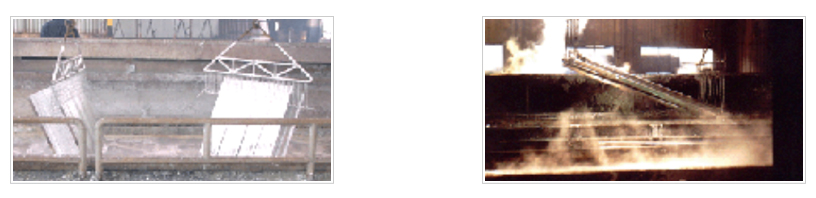
Longer Life |
---|
Melt Zinc coating (Standard 600g/㎡) lasts more than 50 years in rural area, 20-25 years in urban or seashore area without any maintenance. |
Higher Reliability |
---|
Melt Zinc coating makes the iron and zinc integrated in the boundary to improve the life and reliability for the anti-corrosion property. |
Durability |
---|
The coated layer gets very strong as it is in alloy condition and hence is very resistant against any shock from transports or constructional uses. |
Anti Corrosion Property |
---|
Even if there is any partial break on the coated layer by the outside shock, as the zinc performs active cathode-anti-corrosion function, the iron is protected from the corrosion. |
Easy Inspection |
---|
Beside any other conventional coating method, the inspection on the melt-zinc coating finishes in the coating facility to save the time and the labors. And additionally you can only measure the layer thickness on only one or two point and the thickness of the layer is uniformly even. |
Not Effective to the Physical Properties |
---|
No effect on the iron structures. No damage in the physical properties of the iron. |
Perfect Anticorrosion |
---|
The melt-zinc coating can reach everywhere, including any corner and recess, on the parts and give them perfect anticorrosive function. |
Appearance |
---|
The conventional way of zinc coating gets oxidized from the air contacts when it is pulled out of the coating bath as the job is done in the temperature of 450 to 470℃. Oxidized zinc coating obtains degraded gray color instead of silver-white and the layer loses gloss as it is not finely organized. However, if there is small amount of aluminum applied in the process, the aluminum primarily reacts with the air as its affinity is much stronger than zinc when coated products are pulled out of the coating bath and it creates Al203 layer on the zinc coating surface. The oxidized aluminum layer is very thin however it is very finely organized and secure. Once Al203 layer was formed on the surface of zinc coating, it protects the oxidization of the layer and hence the zinc maintains its own color and gloss. Additionally since the aluminum make the size of spangle smaller the gully area from the spangle and its contact surface gets smaller to form a uniformed-evenness coating surface. |
First Acid Treatment |
---|
15 to 20% of hydrochloric acid shall be applies for about 30 minutes in the acid temperature of 28℃. |
Water Cleaning |
---|
With water, it removes acid residues and iron-bases from the coated products after the acid treatment. |
Second Acid Treatment |
---|
After the water-cleaning 7 to 10% of hydrochloric acid shall be applies in the room temperature in about 5 minutes to fully remove oxidized iron from the coated products. |
Water Cleaning |
---|
Clean the products with water. |
Inspection on the First Treatment |
---|
Inspect the products. Defective parts shall be returned to the acid treatment again. |
After Lox Process |
---|
Since oxidization is generated on the pure iron surface in a brief instant, after-lox process shall be applied to the iron surface to ease the coating by forming a layer on the surface. The combination should be as following: 30% of Zinc chloride + Ammonium chloride in the 80 - 90℃. |
Dry |
---|
Keep the temperature of the coated products as 200℃ to prevent the explosion during the process. |
Coating |
---|
Coating shall be performed in the zinc bath in the temperature of 460℃. By removing oxidizing agent from the products, slowly pull them up out of the bath after 90 seconds of dipping. |
Cooling |
---|
The coated products are cooled down with water to protect themselves from surface oxidization. |
Process Flow |
---|
![]() |